The technology used to manufacture BISALLOY® steel is world-class, as the demands of high-strength, high-hardness steels dictate the need for one of the most stringent process routes used to manufacture steel plate, anywhere in the world.
1) Sinto Shot Blasting (Pre Heat Treatment)
Shot blasting greenfeed plates with steel shot removes scale, rust, and dirt, ensuring even heating and cooling during quenching and preserving optimal flatness.
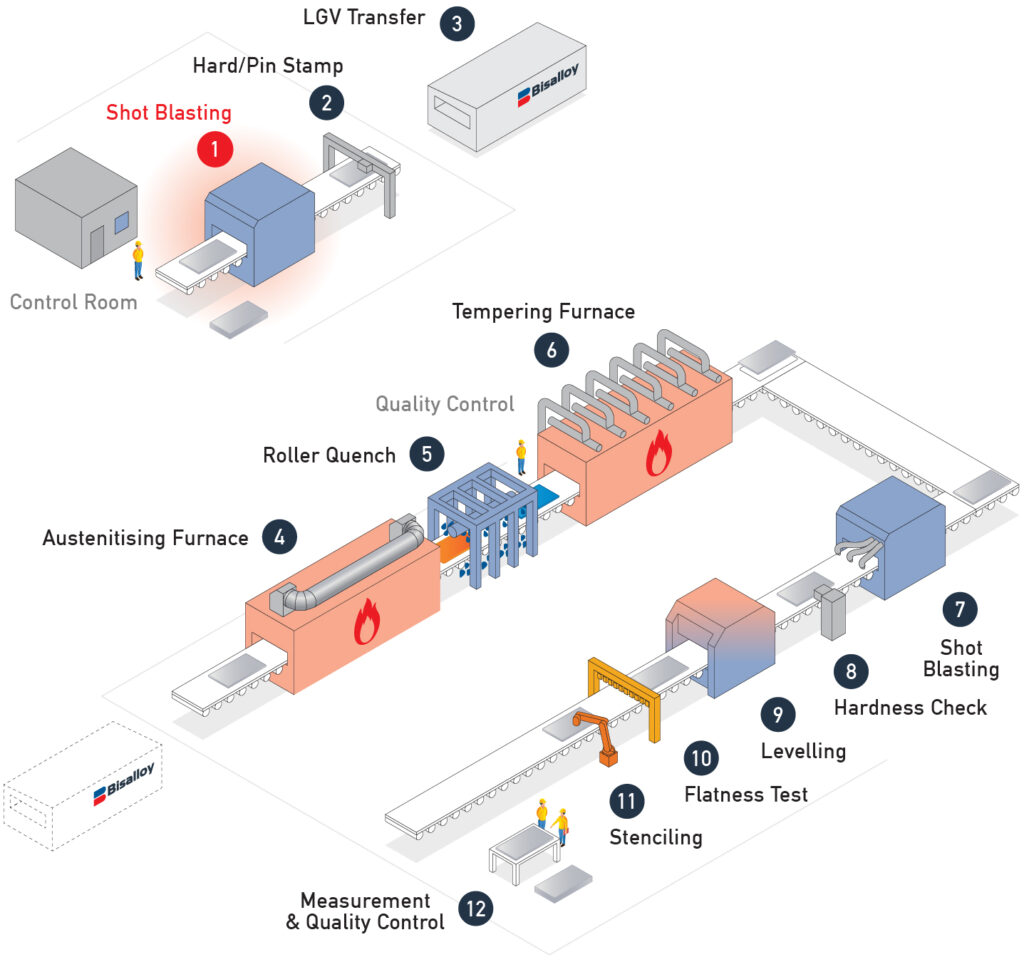
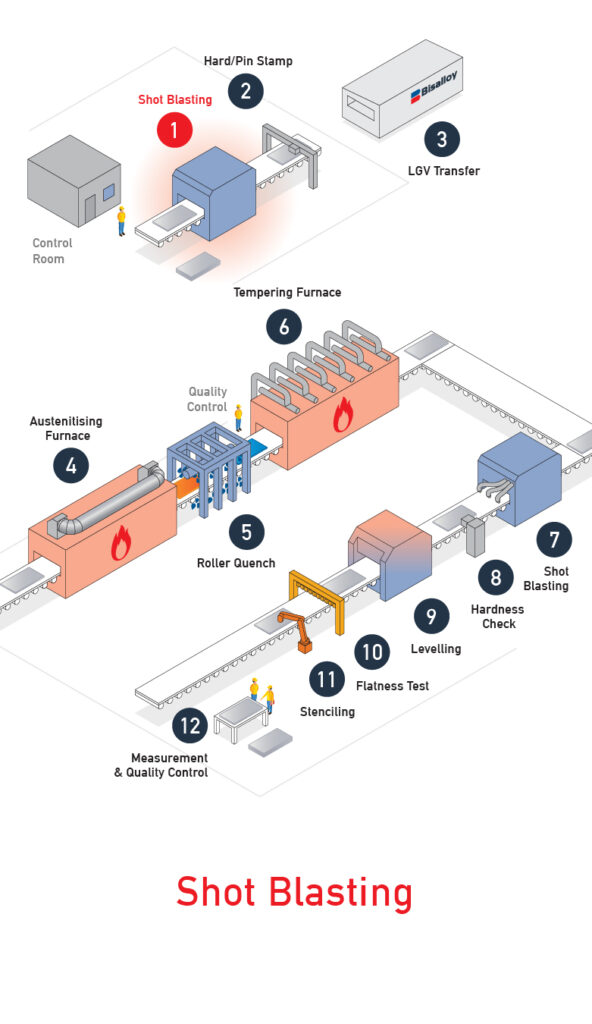
2) Hard/Pin Stamp
Plates are hard-stamped with a unique 6-digit plate number. Bisalloy uses the plate numbers to track & trace the processing of the plate in accordance with the Bisalloy quality assurance system.
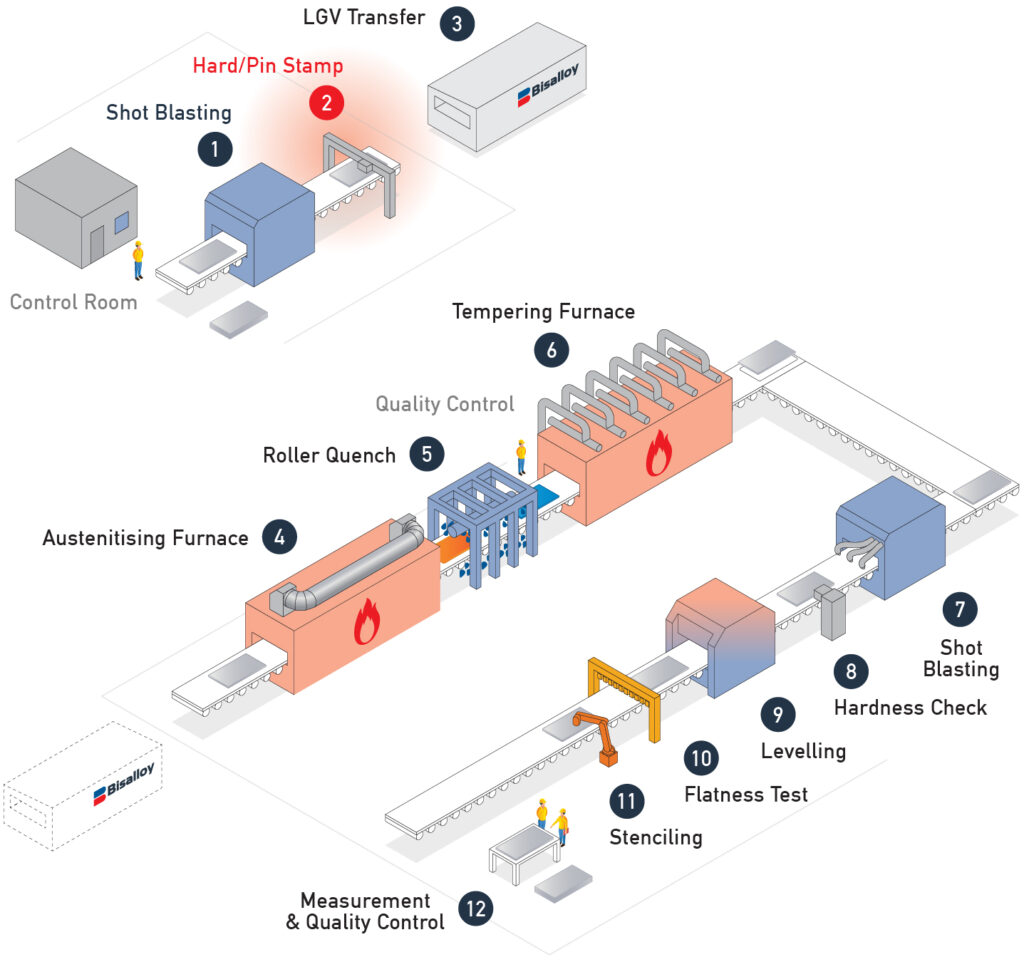
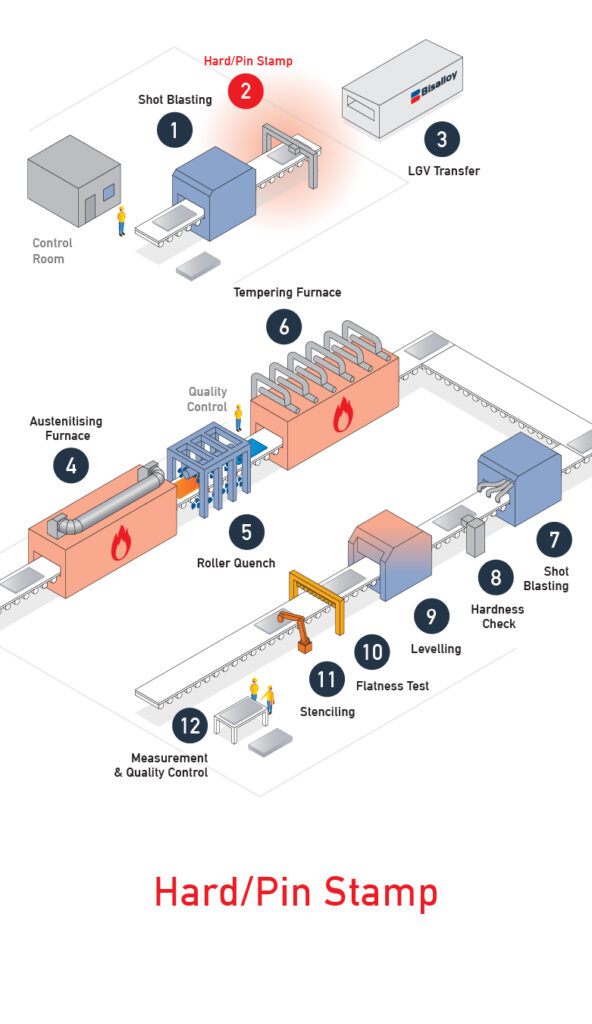
3) LGV Transfer
Plates are transferred between the production lines from building 1 to building 2 with the purpose-built LGV (Laser Guided Vehicle). The LGV automatically shuttles plates between buildings 24 hours a day.
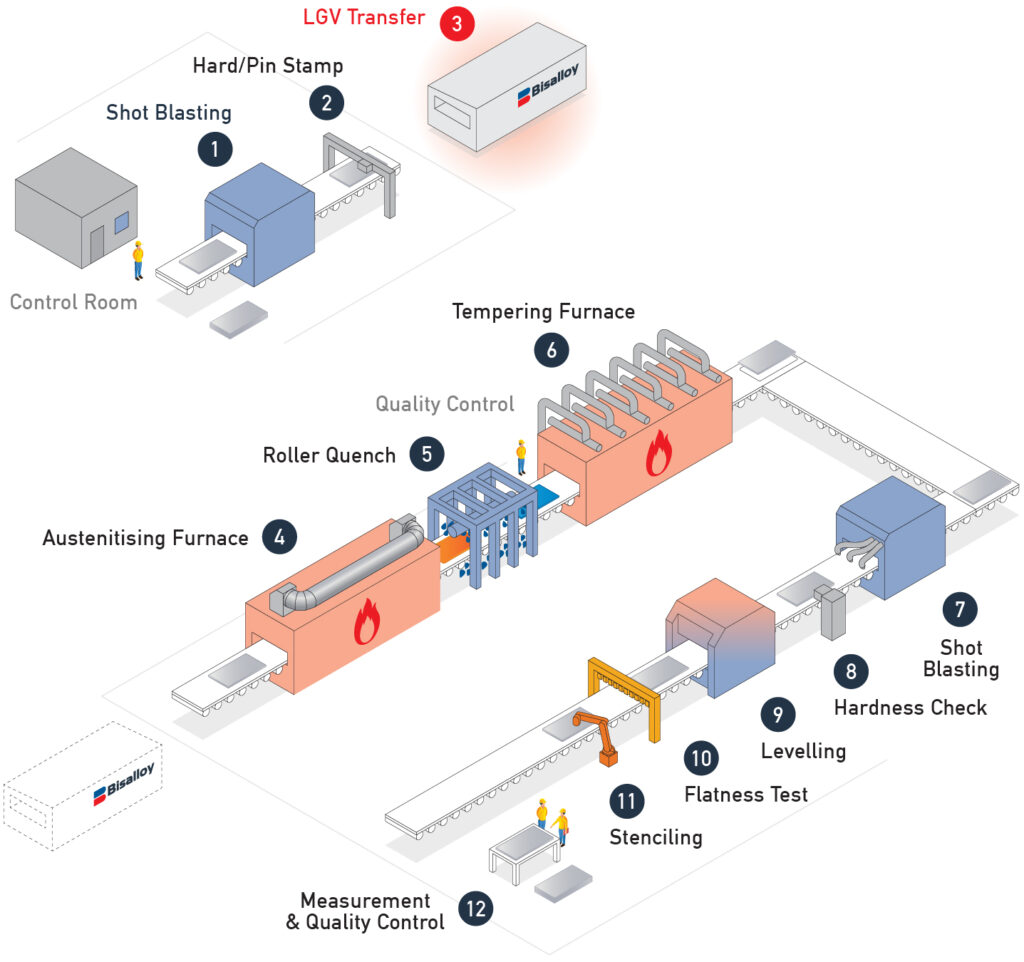
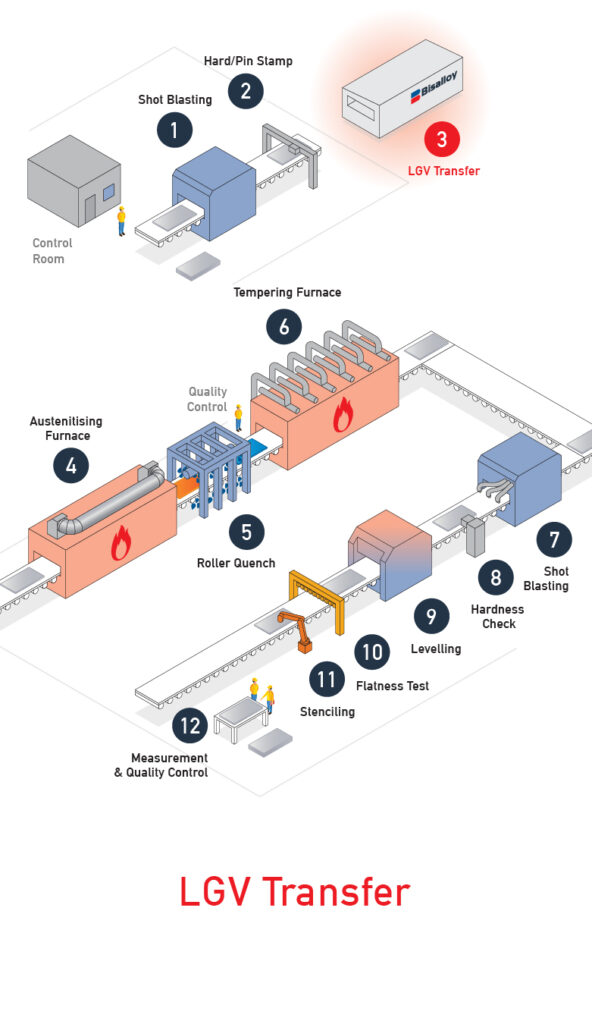
4) Austenitising Furnace
The austenitising furnace heats the plates to 900°C. The time a plate spends in the furnace is dependent on the thickness of the plate. The purpose of heating the plate to 900°C is to change the microstructure in the plate to austenite, which is the ideal microstructure for quenching.
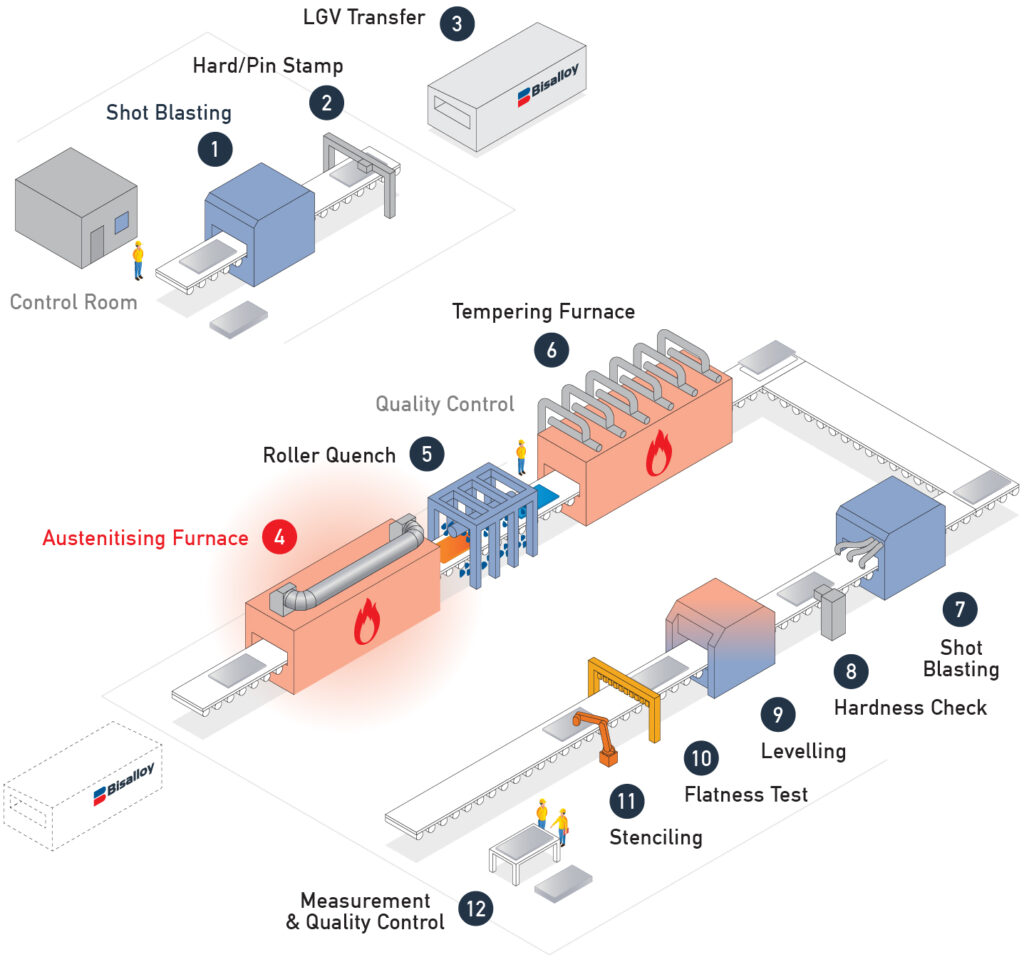
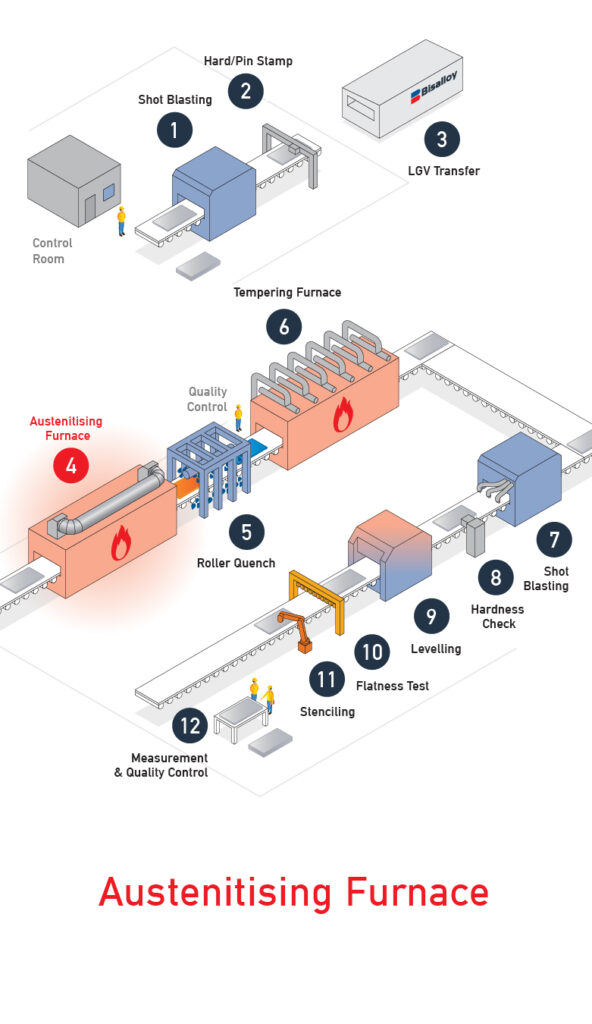
5) Roller Quench
The plate then enters the continuous roller quench unit, where cooled water is delivered to both sides of the plate by a series of high-intensity spray pipes. The plate exits the quench unit at just above room temperature. During the quenching operation, a martensitic microstructure forms.
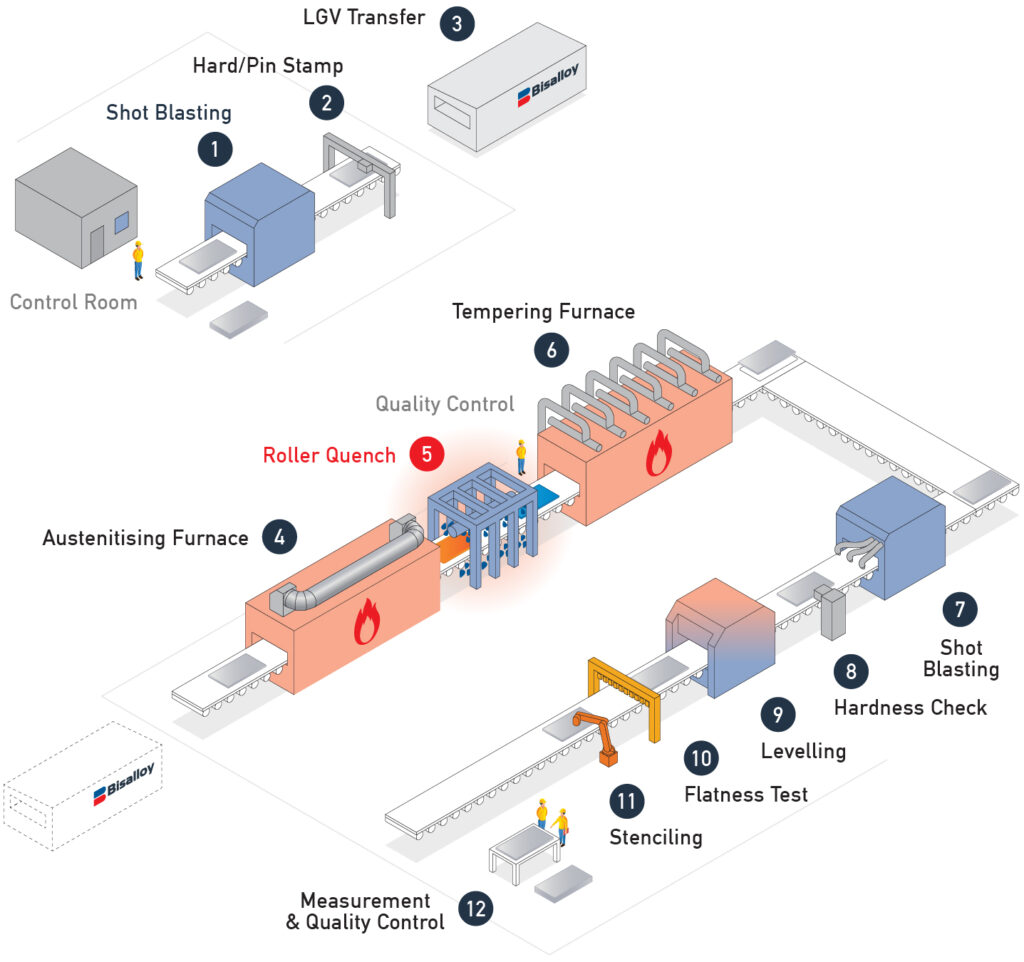
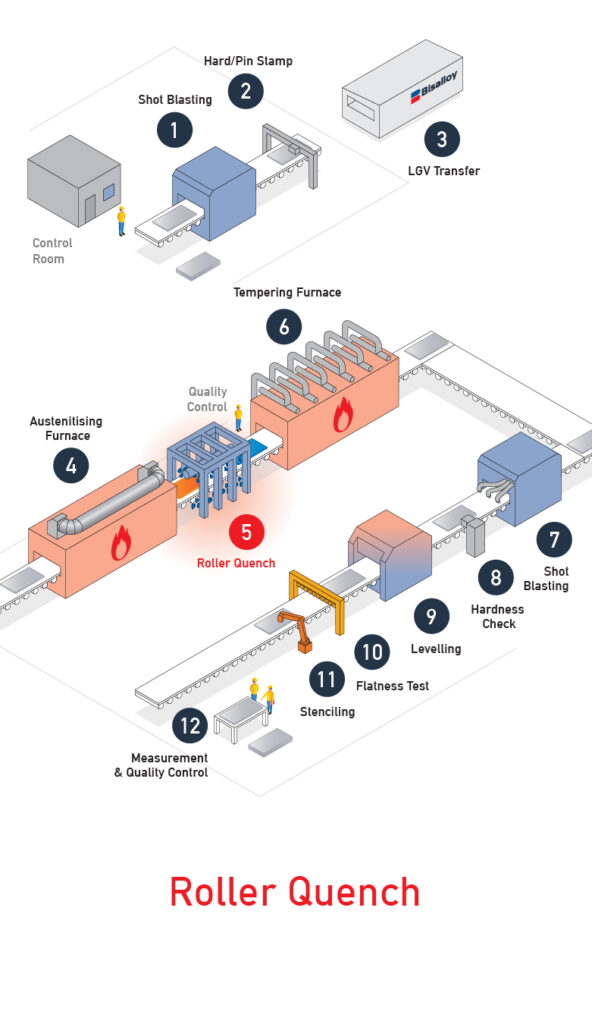
6) Tempering Furnace
Tempering the plate at this stage is conducted to achieve the desired strength, hardness & toughness levels. In general, over the broad range of tempering temperatures, hardness decreases, and toughness increases as the tempering temperature is increased.
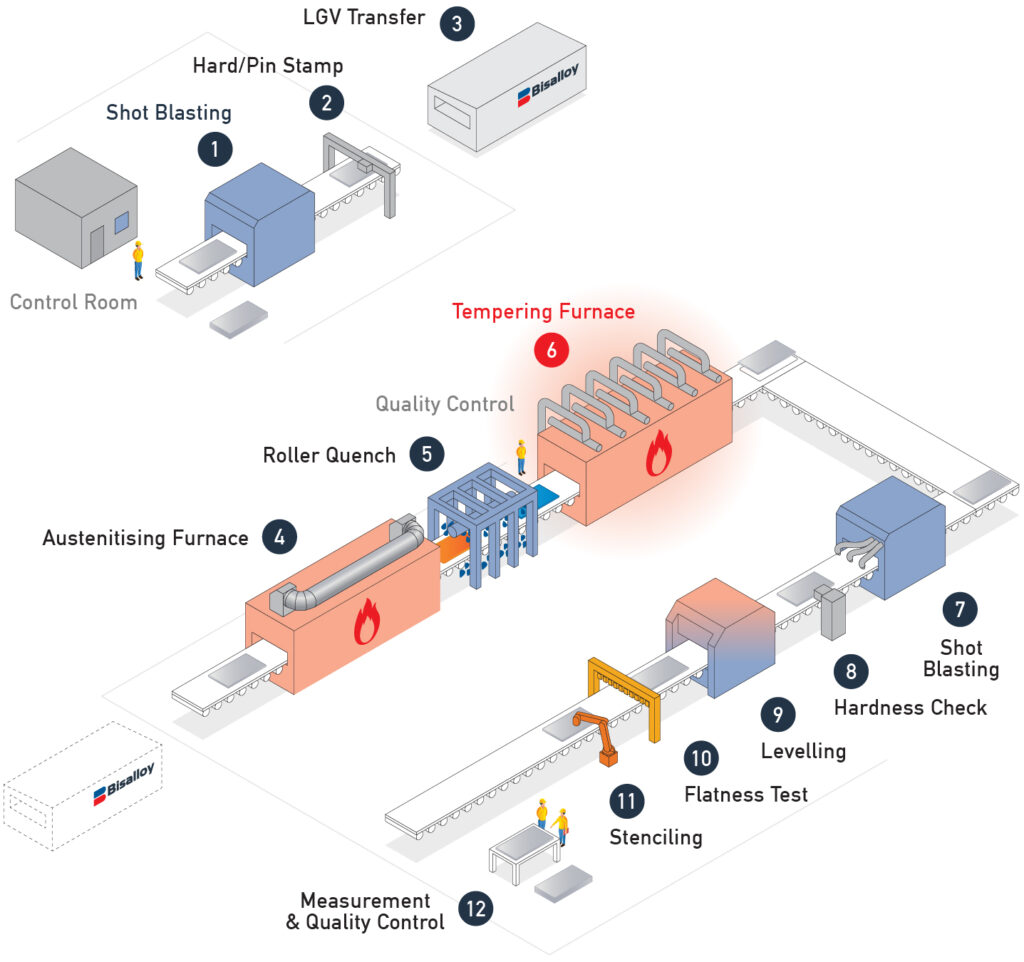
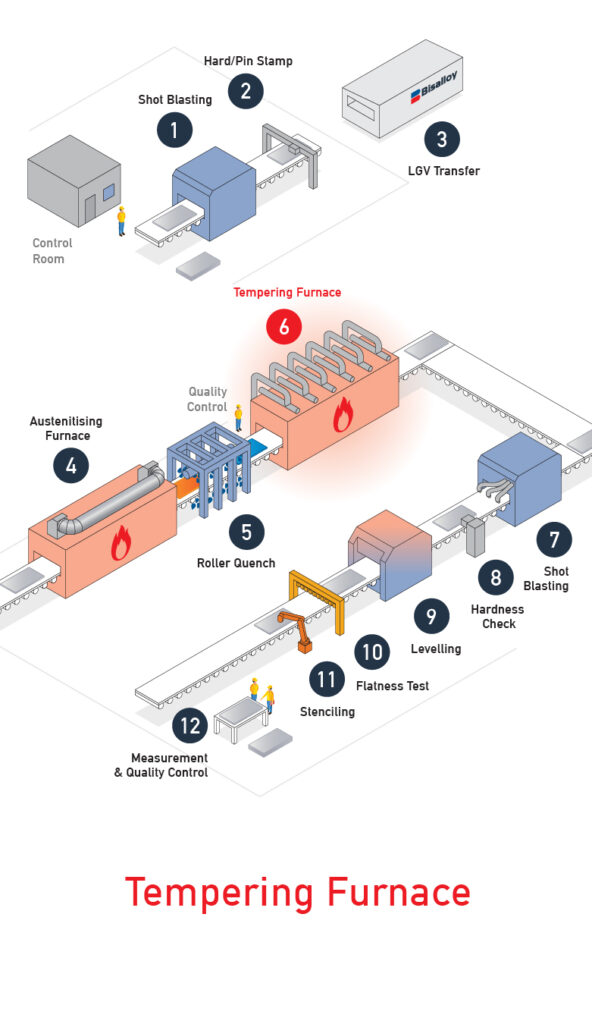
7) Shot Blasting (Post Heat Treatment)
After heat treatment is completed, the plates are then shot blasted in a second shot blaster. This removes any scale formed during heat treatment.
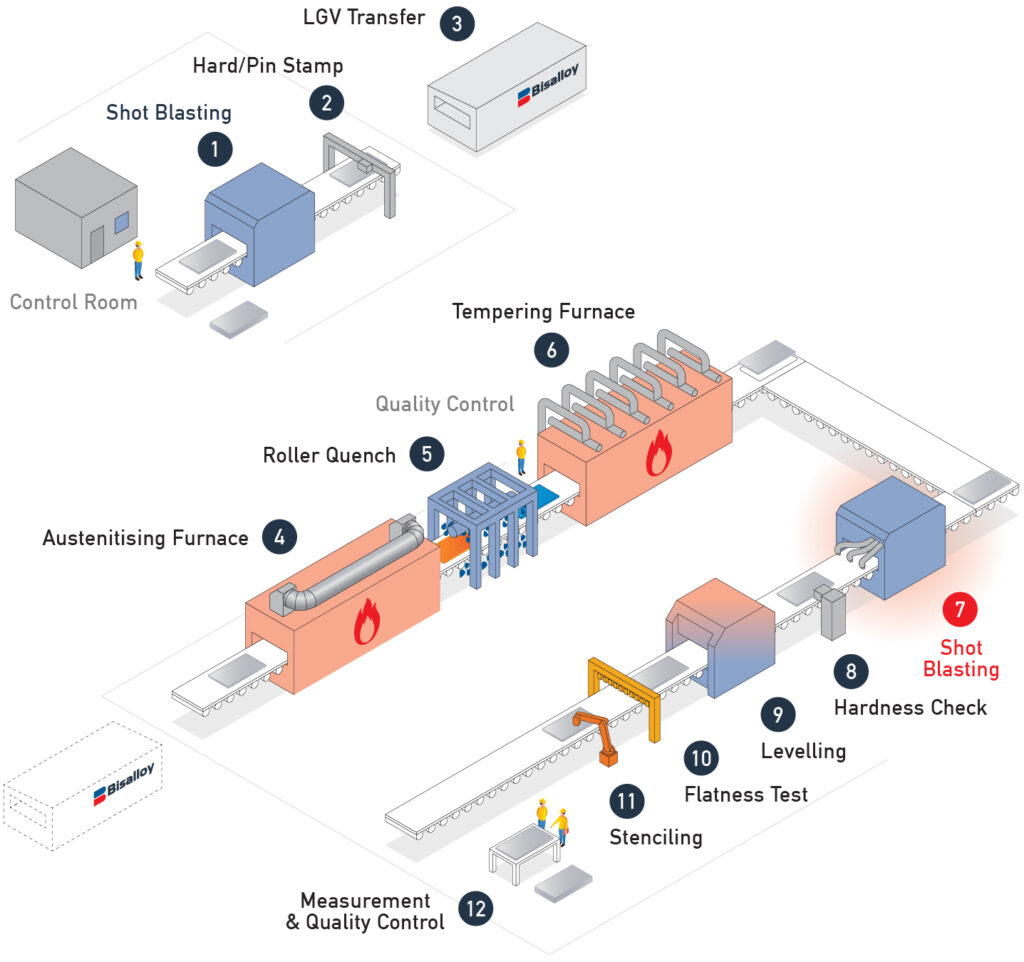
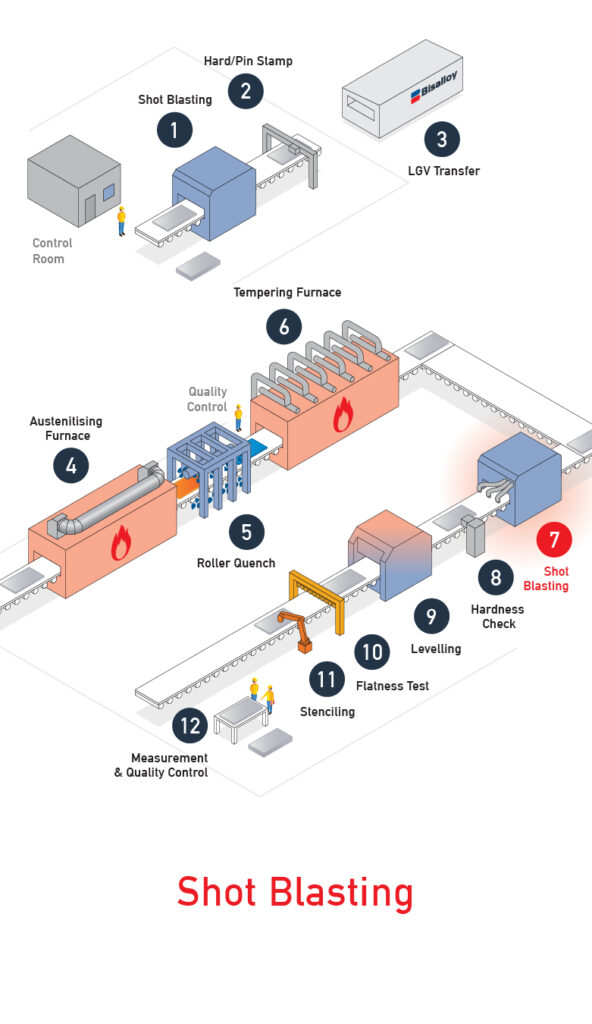
8) Hardness Check
Bisalloy performs hardness tests on every plate produced. This testing procedure is fully automated, including automated milling and indentation, guaranteeing an even greater and more consistent level of accuracy and repeatability.
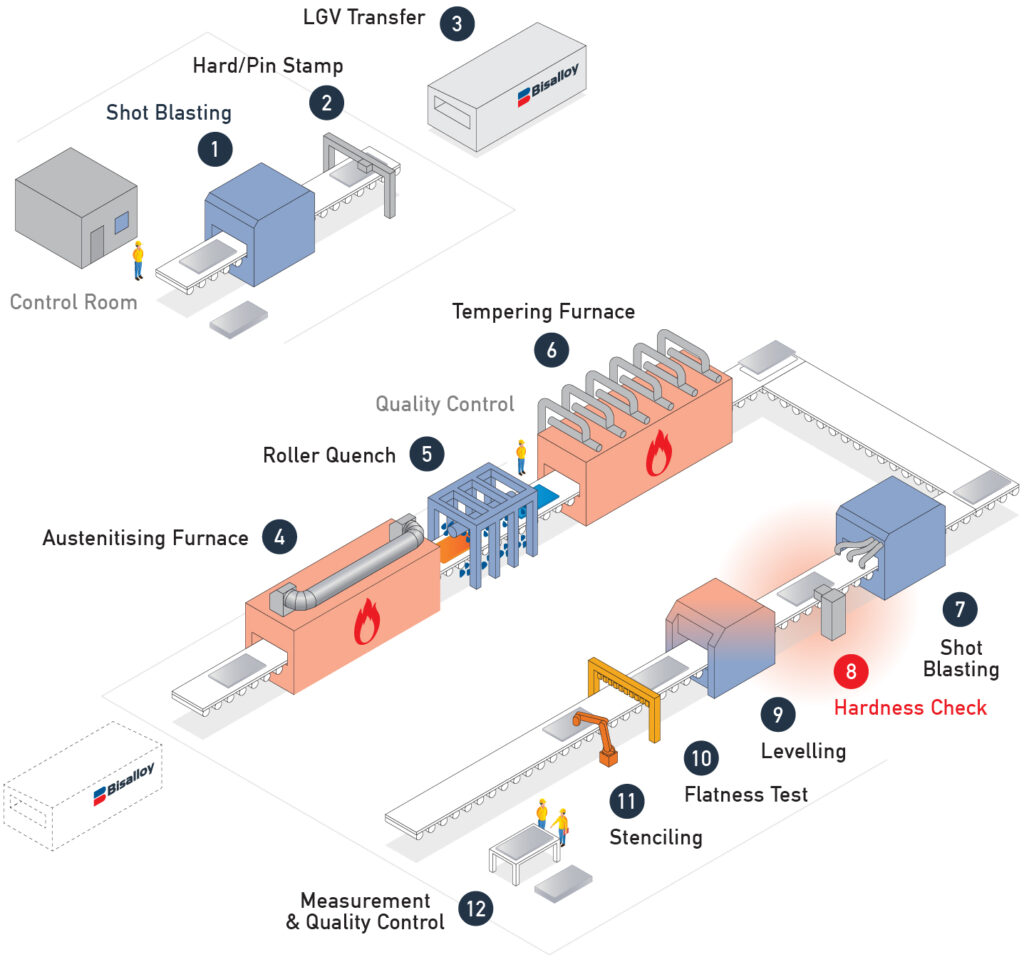
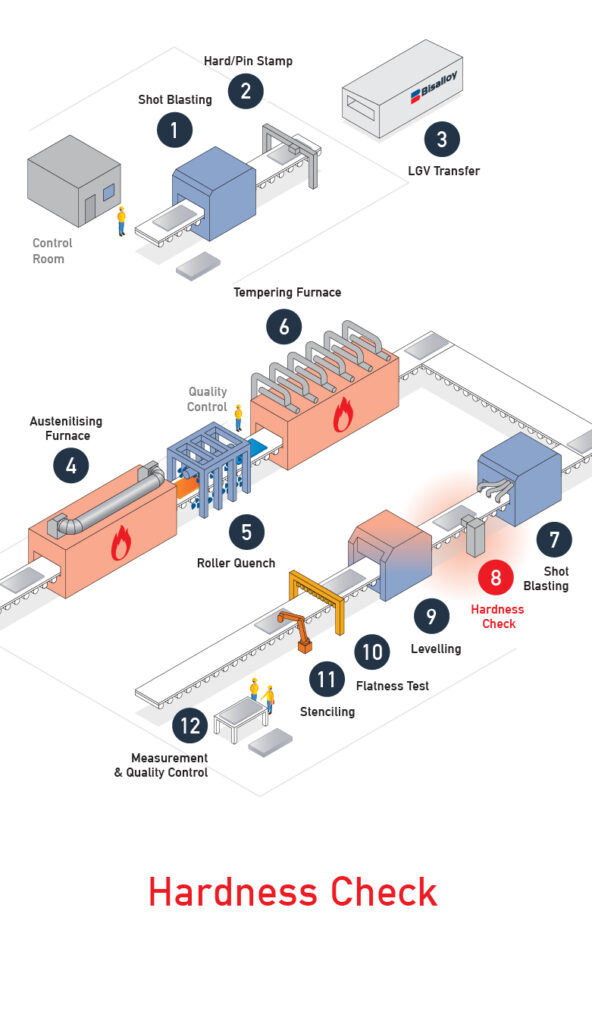
9) Levelling
After the second shot blasting and hardness testing, the plates are then levelled to further improve flatness post-heat treatment.
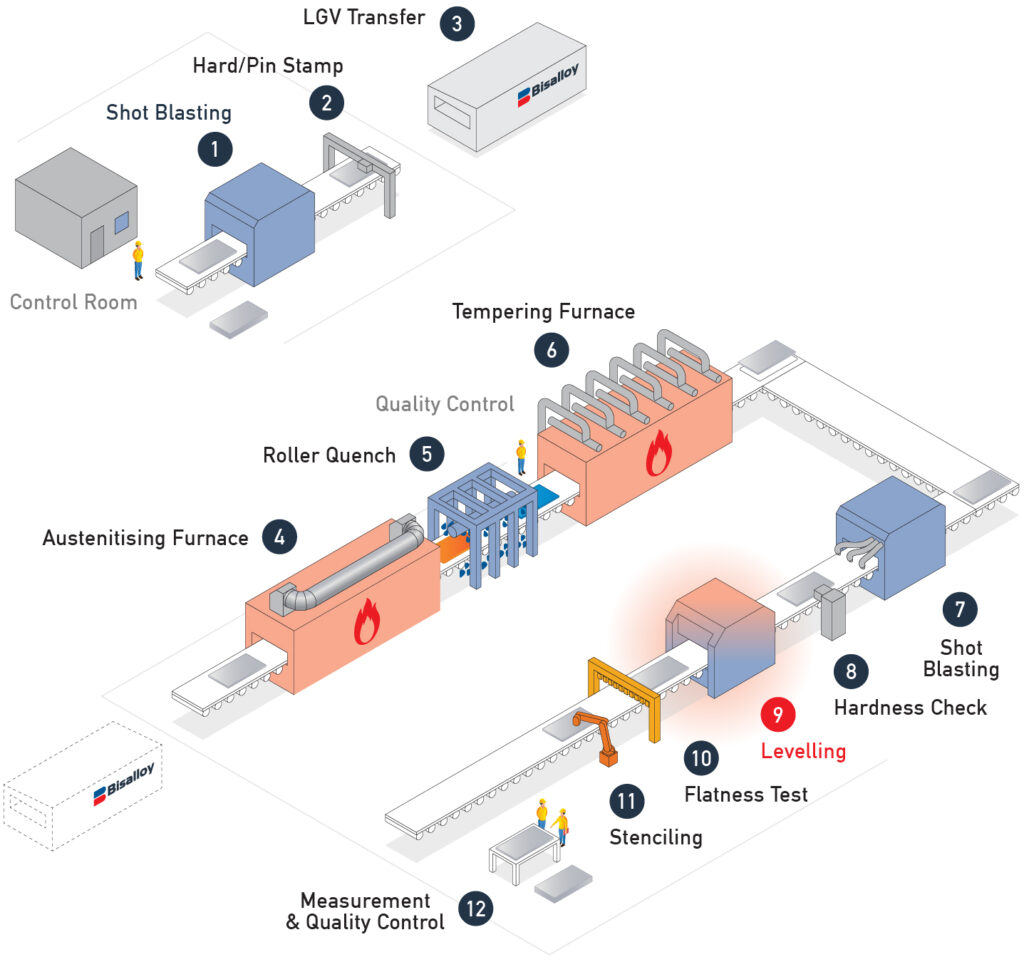
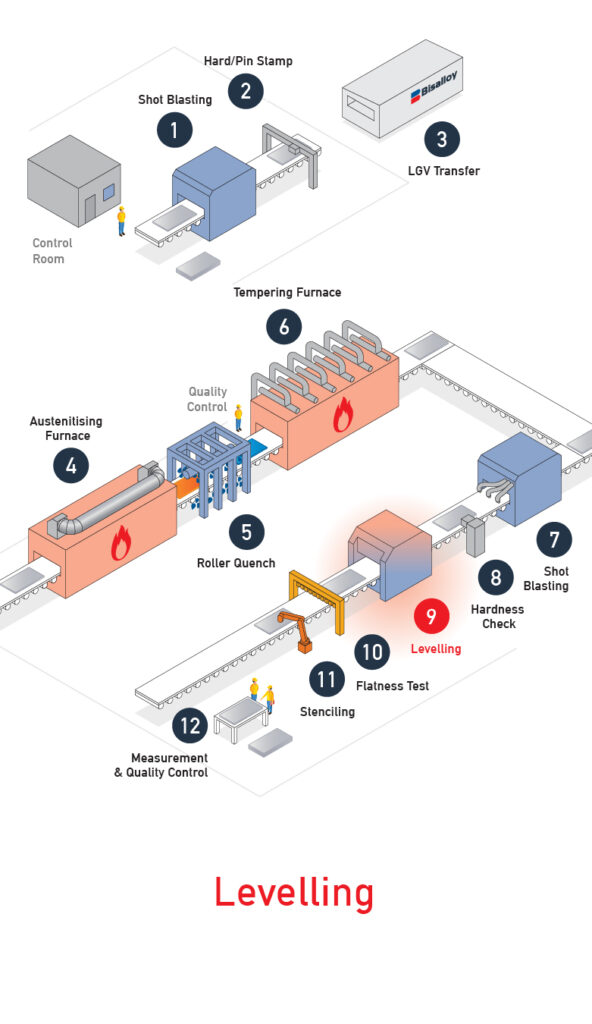
10) Flatness Test
Immediately after the plates are levelled, they run under a laser gate that automatically tests the plate for flatness.
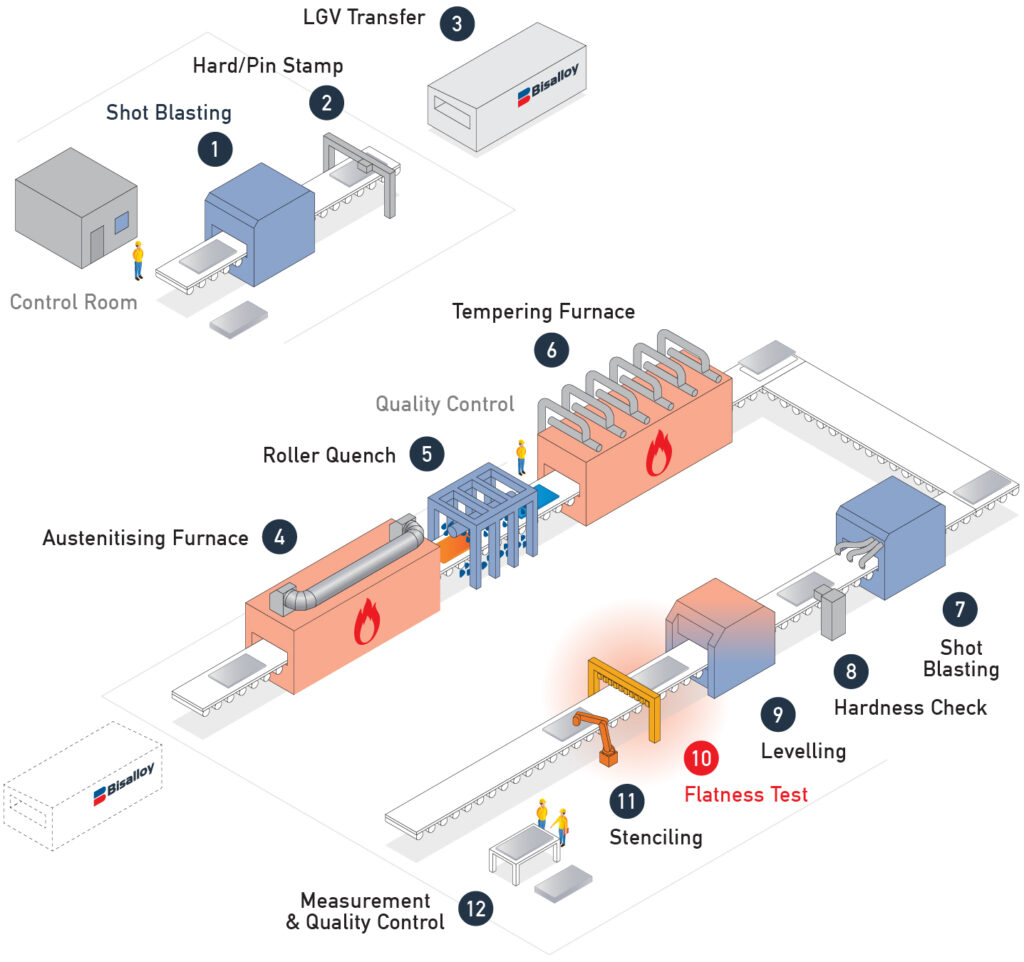
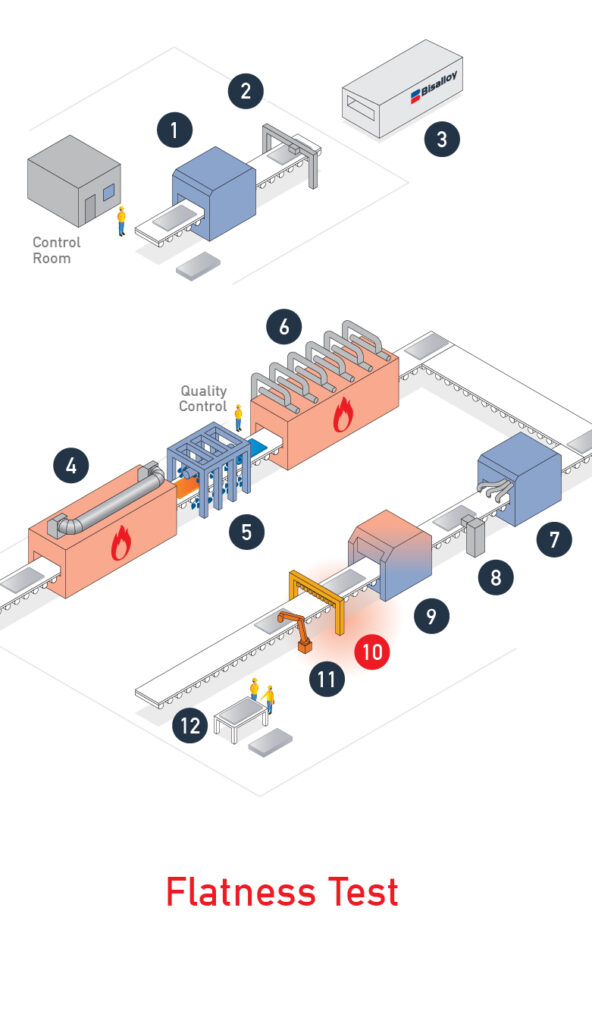
11) Stenciling
In the production line is an automatic stencil arm, which marks on the plate surface the BISALLOY® Steel grade, dimensions and weight.
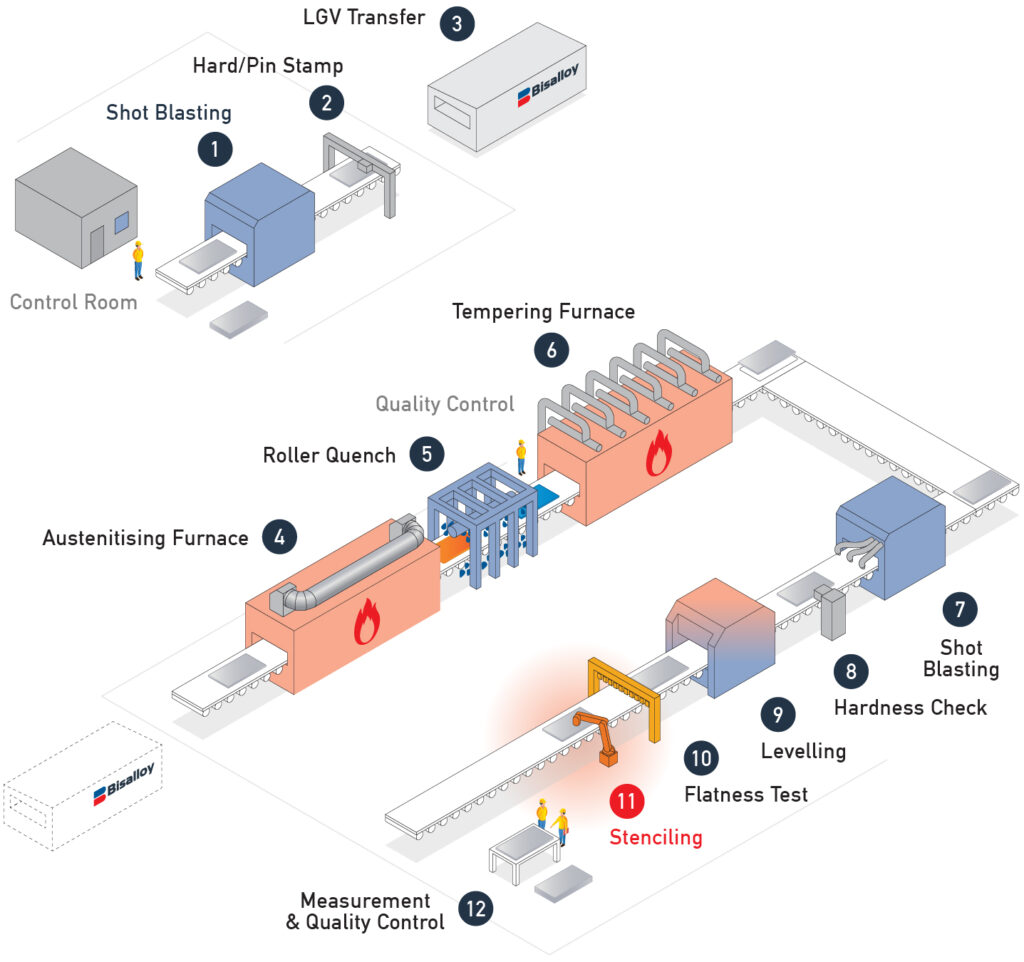
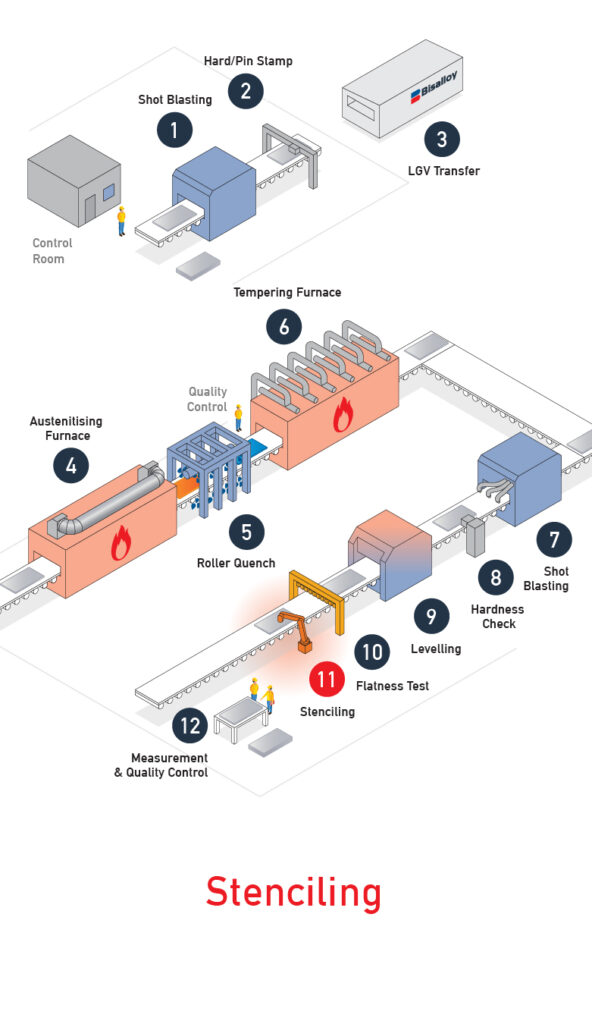
12) Measurement & Quality Control
Plates are now lifted off the production line onto the flatness inspection table, where plates are inspected, which includes surface inspection, dimension checking and test sample cutting.
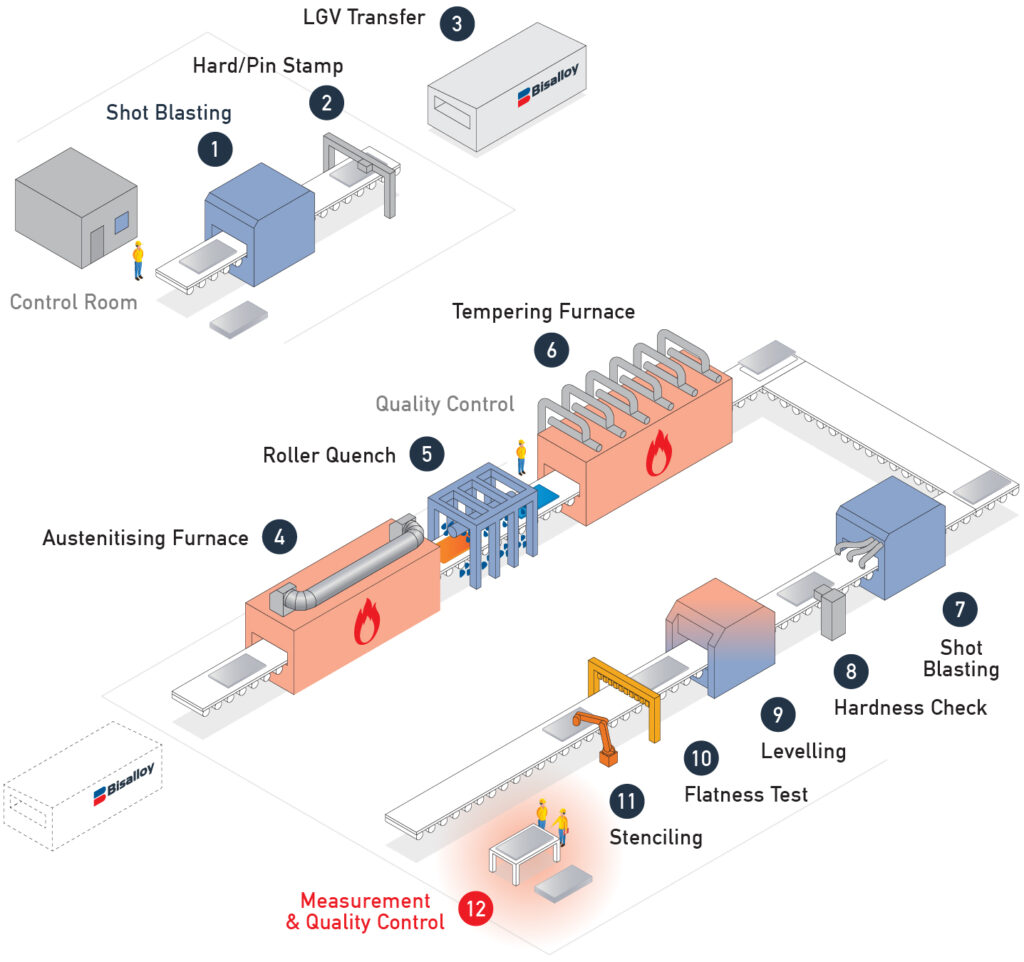
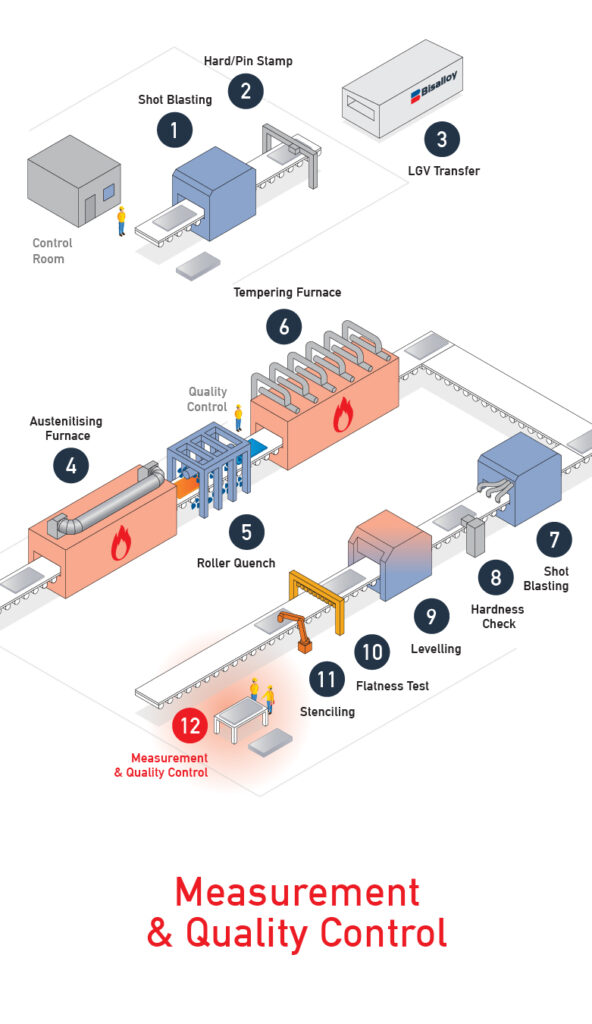
Manufacturing Process
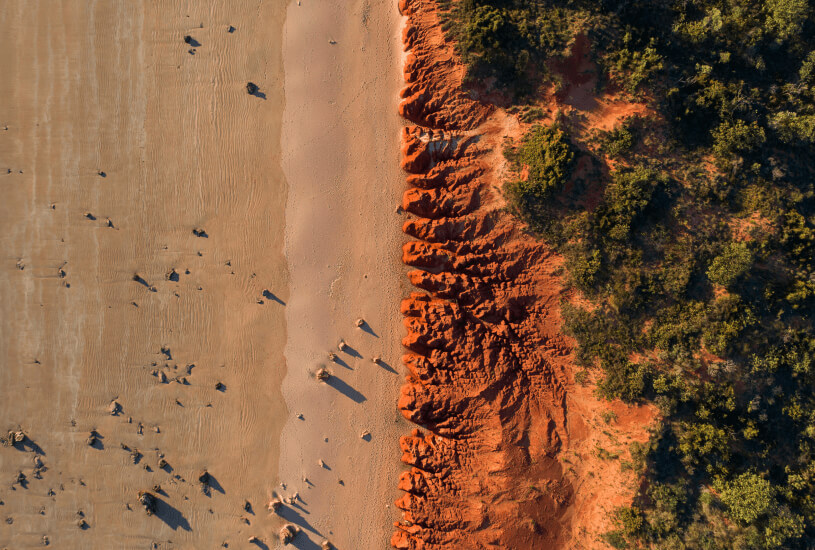
Sustainability
At Bisalloy Steels, we continuously monitor, estimate, and report the energy consumption and greenhouse gas emissions in the manufacturing of BISALLOY® steel products throughout the quenching & tempering process at the Australian production facility.